Increasing implementation of automation in manufacturing and other industries is helping drive the need for new pneumatic component and system designs. In relation to this, customers are looking for solutions which can aid their sustainability efforts as well as those offering data.
Power & Motion spoke with Rex Bateman, Director of Engineering at SMC Corp, about how these trends are influencing developments in the pneumatics industry and how he sees the market performing in the coming year.
*Editor's Note: Questions and responses have been edited for clarity.
Power & Motion (P&M): What trends or market factors do you feel had the largest impacts on pneumatic component and system designs in 2023? Please explain what those trends are and how specifically they impacted the design of pneumatics.
Rex Bateman (RB): As the labor shortage persists, the need for automation in industry continues to rise. Combatting the labor shortage requires more flexibility in automation and lower costs to satisfy the growing demand. With this rise in automation, as well as the increased global awareness and efforts towards sustainability, the need for sustainability in automation is more prevalent than ever; it is now an expectation from customers. The sustainability movement is reducing material choice, which requires innovation from manufacturers to design lighter weight, more compact products using less material. These smaller products not only yield space and material savings, but they also decrease the payload on EOAT (End-of-Arm Tooling), thus yielding energy savings as well.
Customers are also asking for more intelligence, analytics, and integration for all pneumatics that allow for monitoring of machine output so they can spot leaks, manage downtime, and ultimately cut costs. These innovations decrease the power consumption from end users, which is a huge selling point for their own customers. In addition to the expectation to reduce power consumption on the end-user side, there is also an expectation for manufacturers to be more sustainable in the component manufacturing process.
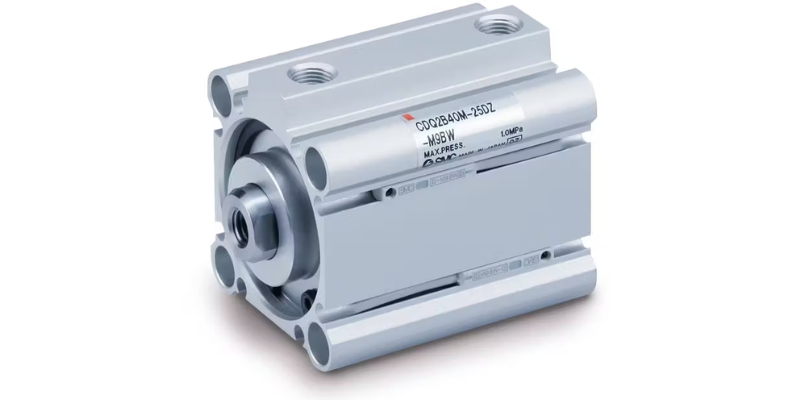
P&M: How have you seen pneumatic component and system designs evolve in recent years?
RB: While most basic components of pneumatic systems are well-established, there are still many innovative ways to evolve these components for specific applications and solutions. One evolution of components is the production of specialized product options to support growing industries, such as the secondary battery industry where material content can affect final product quality and dry atmospheres can negatively affect the life of pneumatic components.
Another example of recent evolution is the ability to integrate industrial networking into control products such as valve manifolds, electro-pneumatic regulators, pressure and flow sensors, etc. In the age of Industrial Internet of Things (IIoT), system operators demand easy-to-maintain systems that allow remote control of components and analytics to track performance and prevent downtime. SMC Corp.’s new Air Management System, the AMS Series, satisfies these demands and more.
P&M: What are some of the key features or performance attributes your company is working to include with its pneumatic components and systems, or for which customers are asking?
RB: SMC Corp.’s Air Management System, the AMS Series, is a game changer for customers that are concerned with energy savings, predictive maintenance, and ease of installation. Instead of simply controlling the air pressure at a machine’s inlet, the AMS Series sends data via OPC-UA that can be used to monitor the overall health of the machine and has features to automatically adjust air pressure during downtime to improve energy savings.
The AMS Series has other built-in features like wireless connectivity, EtherNet IP, and IO-Link to make installations flexible.
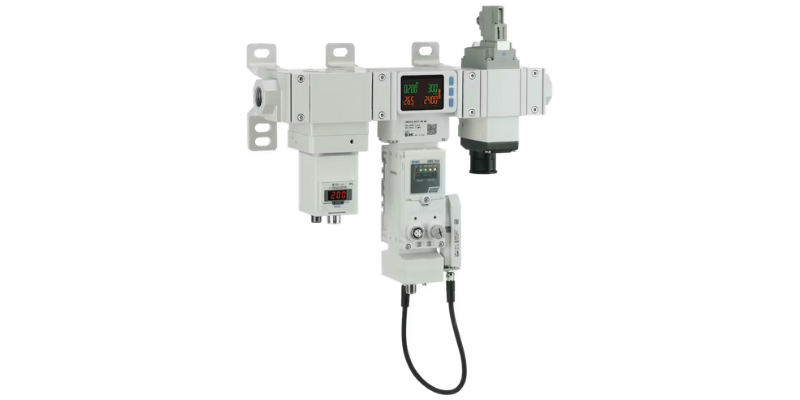
P&M: How much, if at all, are you seeing electronic alternatives taking the place of pneumatic components or systems? Can you offer some examples, and how you possibly see this trend progressing?
RB: In general, it seems that there is a growing interest in electric alternatives for pneumatic components and systems. However, the choice between pneumatic and electric actuators requires the evaluation of application, performance, component costs, system costs, and productivity gains.
When designers require more controllability and precision in applications, electric solutions may be ideal; SMC Corp. has introduced numerous electronic solutions for these specific applications. However, SMC Corp. has also improved pneumatic actuators to increase controllability in positioning, speed, acceleration and deceleration, and these solutions continue to have certain advantages over electric solutions.
Pneumatic advantages versus electric:
- Initial cost (gap is closing)
- Quicker cycle times
- Easier setup and installation (generally)
- Ability to absorb shock loads
- More output power in a smaller package
Electric advantages versus pneumatic:
- Easily set multiple and repeatable positions
- More energy efficient while moving; idle state consumes electricity where pneumatics does not
- Repeatable control of speed, acceleration, and deceleration
- More diagnostics to assist troubleshooting
- Longer life if operated correctly (no seals to wear)
P&M: Are you seeing a greater integration of electronics with pneumatics? If so, what are some examples you can share and the benefits of doing so?
RB: The integration of electronics with pneumatics has been a growing trend for the past few decades with companies that consistently listen to customer feedback and practice R&D. As technology advances, it becomes easier and less costly to combine electronics and pneumatics, and now there are more components in the market that are hybrid than strictly electronic or pneumatic.
The advantages of these hybrid solutions are simple: electronics provide superior control and feedback while pneumatics provide the necessary force and speed for applications at a reasonable cost. The caveat, however, is that the integration of pneumatics requires adjustments in the system and clean, dry air, whereas a strictly electronic system would only require plug-and-play.
P&M: Do you foresee any new trends or market factors impacting pneumatic designs in the coming year or years? If so, what are those and what impact will they have?
RB: The industry standards for automation will continue to rise as demands from the market increase and technology becomes more advanced. The trends in sustainability will continue as well as the focus on safety products as concerns grow for both the well-being of the planet and its people.
We also expect to see the capabilities and integration of AI (artificial intelligence) grow in the coming years. It will become industry standard that hybrid pneumatic and electric products are able to provide data including exact position, pressure, temperature, flow, dew point, etc.
P&M: Are there any economic/market factors you are concerned could negatively impact the pneumatics industry in the coming year?
RB: In 2024, there are some expected economic headwinds: the ongoing labor strikes, an election year, supply chain issues, consequences of over purchasing from 2022-2023, and the continuation of a soft market. More specifically, the semiconductor industry overspent in 2022 and 2023 and is currently experiencing a significant slowdown; it may be late 2024 before it starts to recover.
The automotive industry has some large projects in the works, but many of these may be delayed due to the UAW strike and consumers being reluctant to purchase the EVs that many major companies have gambled billions of dollars on. These projects may remain on hold or even be eliminated in the coming months pending sales.
Food and packaging industries will remain relatively strong but will also experience a slowdown.
P&M: How do you see the pneumatics market in general performing in 2024?
RB: Overall, the market will continue to grow as the need for automation rises due to limited labor and resources. While the market will face economic challenges ahead, we are optimistic; supply chain issues are improving, new demand is surfacing due to inventories being depleted in 2022, and there is opportunity for new market potential and diversification with investments in alternative energy and sustainability that are now being implemented in industry and driving new consumer products to the markets.
By Sara Jensen
Browse pneumatic and hydraulic offerings from SMC Corp.
Article Source:
Power & Motion